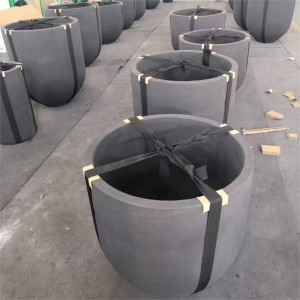
تانبے کی بدبودار کے لئے گریفائٹ مصلوب کی مینوفیکچرنگ ٹکنالوجی ایک انقلاب سے گزر رہی ہے۔ یہ عمل دنیا کے جدید ترین سرد آئسوسٹٹک پریسنگ طریقہ کا استعمال کرتا ہے اور 600MPA کے اعلی دباؤ کے تحت تشکیل دیا گیا ہے تاکہ یہ یقینی بنایا جاسکے کہ مصلوب کی داخلی ڈھانچہ یکساں اور عیب سے پاک ہے اور اس میں انتہائی اعلی طاقت ہے۔ یہ جدت نہ صرف مصیبت کی کارکردگی کو بہتر بناتی ہے ، بلکہ توانائی کے تحفظ اور ماحولیاتی تحفظ میں ایک اہم پیشرفت بھی کرتی ہے۔
سرد isostatic دباؤ کے فوائد
داخلی ڈھانچہ یکساں اور عیب سے پاک ہے
ہائی پریشر مولڈنگ کے تحت ، تانبے کے گرافائٹ کروسیبل کی داخلی ڈھانچہ بغیر کسی نقائص کے انتہائی یکساں ہے۔ یہ روایتی کاٹنے کے طریقوں کے بالکل برعکس ہے۔ کم دباؤ کی وجہ سے ، روایتی طریقے لامحالہ داخلی ساختی نقائص کا باعث بنتے ہیں جو اس کی طاقت اور تھرمل چالکتا کو متاثر کرتے ہیں۔
اعلی طاقت ، پتلی صلیب دیوار
سرد isostatic دبانے کا طریقہ ہائی پریشر کے تحت صلیب کی طاقت کو نمایاں طور پر بہتر بناتا ہے۔ زیادہ سے زیادہ طاقت مصلوب دیواروں کو پتلی بنانے کی اجازت دیتی ہے ، اس طرح تھرمل چالکتا میں اضافہ اور توانائی کی کھپت کو کم کرنے میں مدد ملتی ہے۔ روایتی مصلوب کے مقابلے میں ، اس نئی قسم کی صلیبی صلاحیت موثر پیداوار اور توانائی کی بچت کی ضروریات کے لئے زیادہ موزوں ہے۔
عمدہ تھرمل چالکتا اور کم توانائی کی کھپت
پگھلے ہوئے تانبے کے گریفائٹ مصلوب کی اعلی طاقت اور پتلی دیواروں والی ساخت کا نتیجہ روایتی مصلوب کے مقابلے میں نمایاں طور پر بہتر تھرمل چالکتا کا نتیجہ ہے۔ تھرمل چالکتا کو بہتر بنانے کا مطلب یہ ہے کہ ایلومینیم مرکب ، زنک مرکب ، وغیرہ کے بدبودار عمل کے دوران گرمی کو زیادہ یکساں اور تیزی سے منتقل کیا جاسکتا ہے ، جس سے توانائی کی کھپت کو کم کیا جاسکتا ہے اور پیداواری کارکردگی کو بہتر بنایا جاسکتا ہے۔
روایتی مینوفیکچرنگ کے طریقوں سے موازنہ
کاٹنے کے طریقوں کی حدود
گھریلو طور پر تیار کردہ گریفائٹ مصلوب کا بیشتر حصہ کاٹ کر اور پھر sintering کے ذریعے بنایا جاتا ہے۔ اس طریقہ کار کے نتیجے میں دباؤ کم ہونے کی وجہ سے ناہموار ، عیب دار اور کم طاقت والے داخلی ڈھانچے ہوتے ہیں۔ اس کے علاوہ ، اس میں تھرمل چالکتا اور اعلی توانائی کی کھپت ہے ، جس کی وجہ سے اعلی کارکردگی اور توانائی کی بچت کے ل modern جدید صنعت کی ضروریات کو پورا کرنا مشکل ہوجاتا ہے۔
تقلید کرنے والوں کے نقصانات
کچھ مینوفیکچررز مصلوب پیدا کرنے کے ل cold ٹھنڈے آئسوسٹٹک دبانے کے طریقہ کار کی نقل کرتے ہیں ، لیکن ناکافی مینوفیکچرنگ پریشر کی وجہ سے ، ان میں سے بیشتر سلیکن کاربائڈ مصلوب پیدا کرتے ہیں۔ ان مصلوبوں میں موٹی دیواریں ، ناقص تھرمل چالکتا اور اعلی توانائی کی کھپت ہوتی ہے ، جو سرد آئوسوسٹٹک دبانے سے پیدا ہونے والے اصلی پگھلے ہوئے تانبے کے گریفائٹ مصلوب سے بہت دور ہیں۔
تکنیکی اصول اور درخواستیں
ایلومینیم اور زنک مرکب کے بدبودار عمل میں ، آکسیکرن مزاحمت اور مصیبت کی تھرمل چالکتا اہم عوامل ہیں۔ کولڈ آئسوسٹٹک پریسنگ کے طریقہ کار کا استعمال کرتے ہوئے تیار کردہ مصلوب آکسیکرن مزاحمت پر خصوصی زور دیتے ہیں جبکہ فلورائڈ پر مشتمل بہاؤ کے منفی اثرات سے گریز کرتے ہیں۔ یہ مصلوب دھات کو آلودہ کیے بغیر اعلی درجہ حرارت پر عمدہ کارکردگی کو برقرار رکھتے ہیں ، استحکام کو نمایاں طور پر بہتر بناتے ہیں۔
ایلومینیم کھوٹ میں سملٹنگ میں درخواست
گریفائٹ کروسیبل ایلومینیم مرکب کے پگھلنے میں خاص طور پر ڈائی کاسٹنگ اور کاسٹنگ کی تیاری میں اہم کردار ادا کرتا ہے۔ ایلومینیم کھوٹ کا پگھلنے والا درجہ حرارت 700 ° C اور 750 ° C کے درمیان ہے ، جو درجہ حرارت کی حد بھی ہے جہاں گریفائٹ آسانی سے آکسائڈائزڈ ہوتا ہے۔ لہذا ، اعلی درجہ حرارت پر عمدہ کارکردگی کو یقینی بنانے کے ل cold سردی isostatic دباؤ کے ذریعہ تیار کردہ گریفائٹ مصلوب آکسیکرن مزاحمت پر خصوصی زور دیتے ہیں۔
پگھلنے کے مختلف طریقوں کے لئے ڈیزائن کیا گیا ہے
گریفائٹ کروسیبل مختلف قسم کے بدبودار طریقوں کے لئے موزوں ہے ، جس میں گرمی کے تحفظ کے ساتھ مل کر سنگل فرنسٹ سونگھ اور بدبودار بھی شامل ہے۔ ایلومینیم کھوٹ کاسٹنگ کے ل the ، مصیبت کے ڈیزائن کو H2 جذب اور آکسائڈ مکسنگ کو روکنے کی ضروریات کو پورا کرنے کی ضرورت ہے ، لہذا ایک معیاری مصلوب یا بڑے منہ کے پیالے کے سائز کا کروسبل استعمال کیا جاتا ہے۔ سنٹرلائزڈ بدبودار بھٹیوں میں ، جھکاو کرنے والی صلیبی بھٹیوں کو عام طور پر بدبودار فضلہ کو ری سائیکل کرنے کے لئے استعمال کیا جاتا ہے۔
کارکردگی کی خصوصیات کا موازنہ
اعلی کثافت اور تھرمل چالکتا
سرد آئسوسٹٹک دبانے کے ذریعہ تیار کردہ گریفائٹ مصلوب کی کثافت 2.2 اور 2.3 کے درمیان ہے ، جو دنیا میں مصلوبوں میں سب سے زیادہ کثافت ہے۔ یہ اعلی کثافت مصلی زیادہ سے زیادہ تھرمل چالکتا فراہم کرتی ہے ، جو دوسرے برانڈز کے مقابلے میں نمایاں طور پر بہتر ہے۔
گلیز اور سنکنرن مزاحمت
پگھلا ہوا ایلومینیم گریفائٹ کروسیبل کی سطح خصوصی گلیز کوٹنگ کی چار پرتوں کے ساتھ ڈھکی ہوئی ہے ، جو گھنے مولڈنگ میٹریل کے ساتھ مل کر ، کروسبل کی سنکنرن مزاحمت کو بہت بہتر بناتی ہے اور اس کی خدمت کی زندگی کو بڑھا دیتی ہے۔ اس کے برعکس ، گھریلو مصلوب کی سطح پر صرف تقویت یافتہ سیمنٹ کی ایک پرت ہوتی ہے ، جو آسانی سے نقصان پہنچا ہے اور اس سے قبل از وقت آکسیکرن کا سبب بنتا ہے۔
ساخت اور تھرمل چالکتا
پگھلا ہوا تانبے کے گریفائٹ کروسیبل قدرتی گریفائٹ کا استعمال کرتے ہیں ، جس میں عمدہ تھرمل چالکتا ہے۔ اس کے برعکس ، گھریلو گریفائٹ مصلوب مصنوعی گریفائٹ کا استعمال کرتے ہیں ، اخراجات کو کم کرنے کے لئے گریفائٹ کے مواد کو کم کرتے ہیں ، اور مولڈنگ کے لئے مٹی کی ایک بڑی مقدار میں اضافہ کرتے ہیں ، لہذا تھرمل چالکتا میں نمایاں کمی واقع ہوتی ہے۔
پیکیجنگ اور درخواست کے علاقے
پیکنگ
پگھلا ہوا تانبے کے گریفائٹ کروسیبل عام طور پر بنڈل اور بھوسے کی رسی کے ساتھ پیک کیا جاتا ہے ، جو ایک آسان اور عملی طریقہ ہے۔
درخواست کے شعبوں میں توسیع
ٹکنالوجی کی مسلسل ترقی کے ساتھ ، گریفائٹ مصلوب کے اطلاق کے شعبوں میں توسیع جاری ہے۔ خاص طور پر ایلومینیم کھوٹ ڈائی کاسٹنگز اور کاسٹنگ کی تیاری میں ، گریفائٹ مصلوب آہستہ آہستہ اعلی معیار کے آٹوموٹو حصوں کی پیداوار کی ضروریات کو پورا کرنے کے لئے روایتی کاسٹ آئرن برتنوں کی جگہ لے رہے ہیں۔
آخر میں
سرد آئسوسٹٹک دبانے کے طریقہ کار کی اطلاق نے تانبے کی گرافائٹ کروسیبل سلیجنگ کی کارکردگی اور کارکردگی کو ایک نئی سطح تک پہنچایا ہے۔ چاہے یہ داخلی ڈھانچے کی یکسانیت ، طاقت یا تھرمل چالکتا ہو ، یہ روایتی مینوفیکچرنگ کے طریقوں سے نمایاں طور پر بہتر ہے۔ اس جدید ٹیکنالوجی کے وسیع پیمانے پر اطلاق کے ساتھ ، گریفائٹ مصلوب کی مارکیٹ کی طلب میں توسیع جاری رہے گی ، اور پوری صنعت کو زیادہ موثر اور ماحول دوست دوستانہ مستقبل کی طرف راغب کرے گی۔
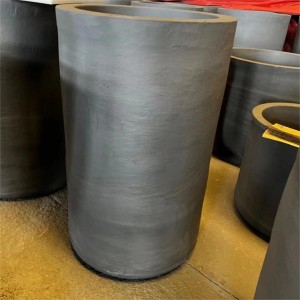
پوسٹ ٹائم: جون -05-2024